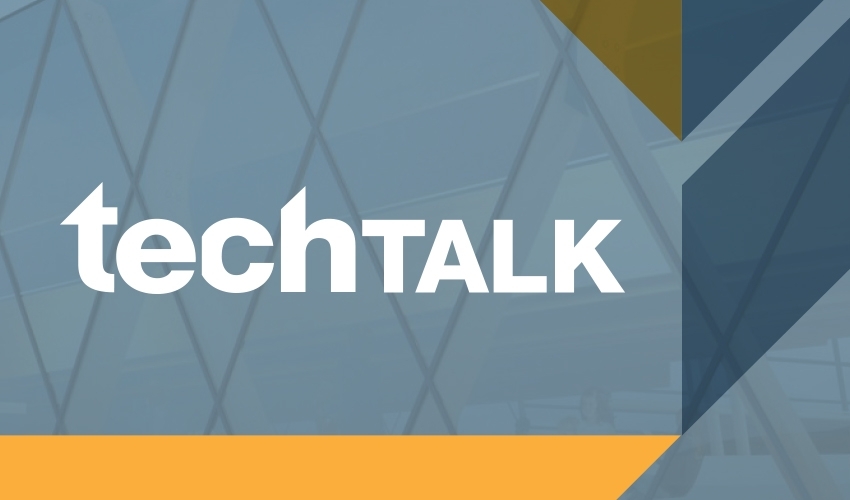
Greetings and welcome to our first newsletter of 2025!
We’re excited to bring you our most recent updates, insights and stories. This issue includes project updates, team news, technical information and much more. I hope you enjoy reading and find the content informative and inspiring.
TechTALK #30 marks a significant milestone. To ensure our quarterly updates meet your needs, we value your feedback. Please take two minutes to complete our survey, and help us shape future issues. Share your preferences, suggest improvements and let us know your reading frequency. Your input is crucial for TechTALK’s development. Access the survey here.
To say thanks, we’re drawing 20 lucky respondents to win a Tech Tower game – perfect for some fun with family and mates. The winners will be drawn on the last day of March and contacted by email, so please ensure you provide your email address.
Thank you for being a valued part of the New Zealand Timber and Construction Industry!
Brett Hamilton – Managing Director
// New Te Ao Mārama whare bridges culture and sustainability at Rangiora High School
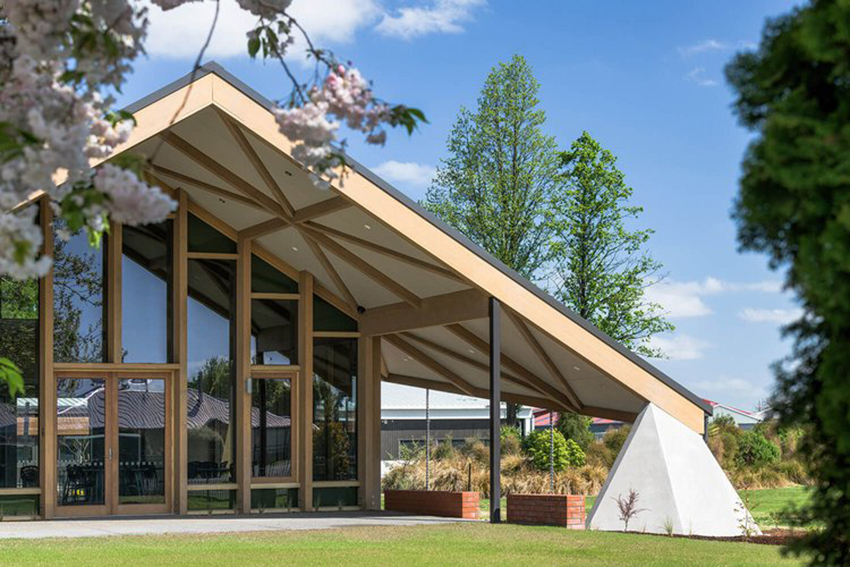
The Techlam team is passionate about every project undertaken, and those supporting student development for the upcoming generation always hold particular meaning. That is why we were especially thrilled to partner with Kobe Construction on the Rangiora High School‘s new whare construction for the manufacture of structural glulam timber components.
Rangiora High School presented an ambitious brief to architects Stufkens + Chambers, who accepted the challenge to design a 176m² learning centre capable of shifting from a classroom for 30-35 students to a performance area accommodating 100, with integrated dining and sleeping facilities.
This $1.8 million fully board-funded flexible cultural hub extended beyond mere construction. It involved designing a space that honoured the school’s cultural heritage while incorporating modern, eco-conscious building techniques.
Exposed timber, chosen for its natural aesthetics and warm atmosphere, became a focal point.
“The main reason to use glulam for this project was the school’s relationship with Māori culture. They wanted this whare to be a warm and welcoming building to all pupils, staff and the community,” William Roberts, co-founder and quantity surveyor at V-Quest, said.
Techlam supplied the fully prefabricated glulam beams and columns. The exposed glulam structure created an expansive, open-plan interior that optimised the building’s multi-functionality, opening onto a sheltered outdoor area.
The design approach reflected biophilic principles, which aim to strengthen the connection between building users and nature through the integration of natural light and natural materials such as timber.
“Mass timber plays a key role in this instance. Exposed natural timber elements bring a sense of warmth and are aesthetically pleasing. There are proven benefits that exposed natural timber supports a range of health improvements, such as stress response, functionality, and psychological well-being. These are great aspects to have for a classroom building,” William explained.
The Techlam glulam pre-fabrication process used digital modelling alongside CNC processing, ensuring precise dimensions (by minimising human error) and faster on-site assembly.
“Mass timber is quick and efficient to install. Using CNC machining means that contractors can easily piece the structure together. The absence of curing times and, in some cases, the need for additional coatings, accelerates the construction process. This speed impacts the overall programme and reduces preliminaries and general (P&G) costs compared to conventional concrete and steel structures,” William added.
From a sustainability standpoint, the selection of glulam was strategic. As an engineered timber material, it requires less embodied energy than steel and concrete, maximising wood usage and minimising the carbon footprint.
“Te Ao Mārama at Rangiora High School demonstrates what can be achieved with sustainable design and mass timber construction. For a relatively small footprint, this project packs a punch, and the glulam canopy and structure really create a warm and inviting learning environment. The design concept was excellent, and the timber choice is perfect,” Blair (Blu) Tipler from Kobe Construction observed.
The building’s placement also holds significance. “Located at the alternative entrance to Rangiora High School, Te Ao Mārama stands out to those entering or passing by. It leaves a lasting impression,” William pointed out.
Te Ao Mārama – which means “the world of enlightenment” and was gifted to the school by Te Ngāi Tūāhuriri Rūnanga – was officially opened with a pōwhiri in October 2024.
// French student sparks transcontinental leap for New Zealand’s engineered timber
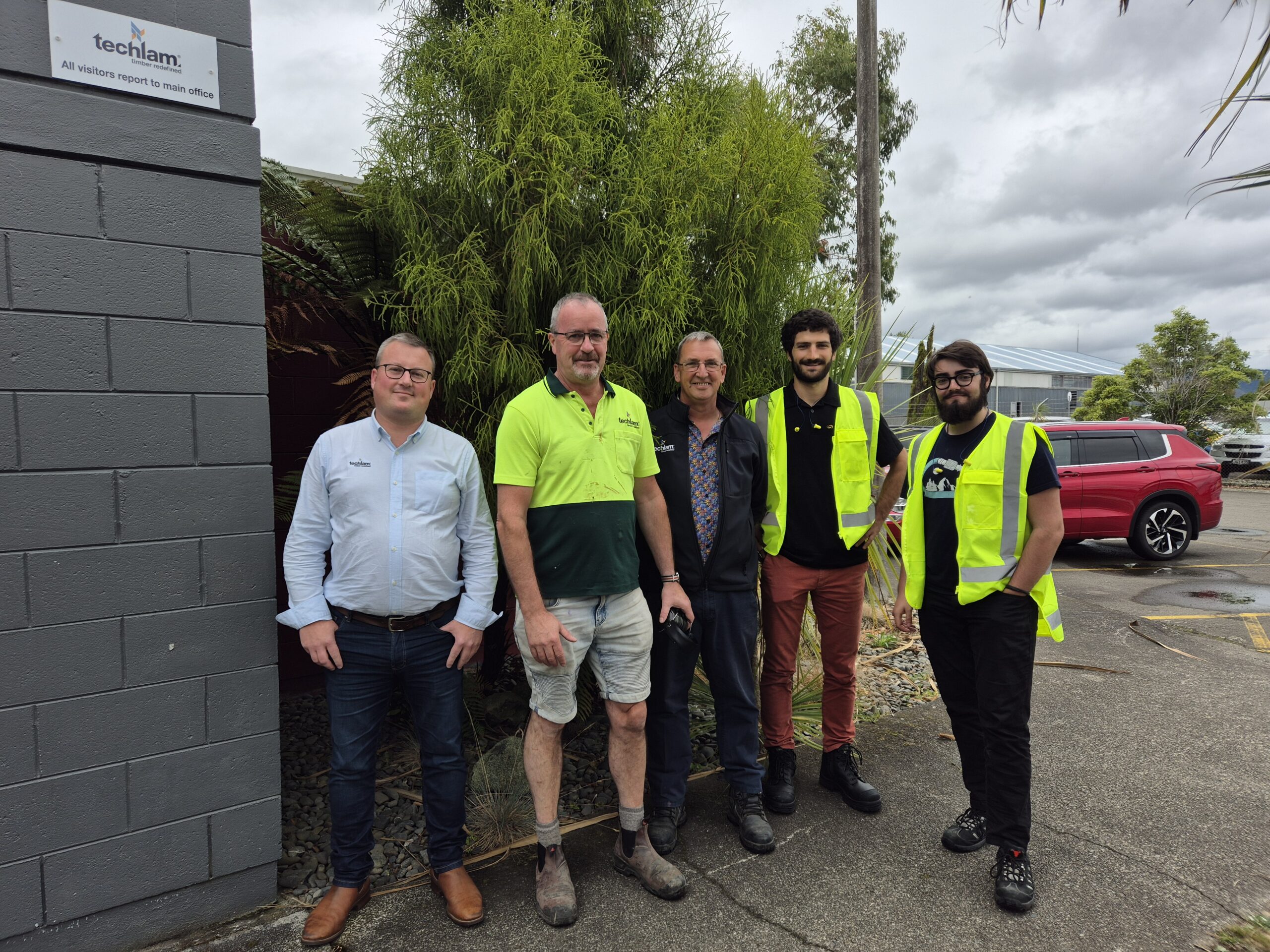
When Jean Margerie arrived at Techlam’s Levin factory from France, he brought more than just his engineering expertise – he represented a unique collaboration between New Zealand’s wood industry and European technical education.
The partnership, connecting Techlam with New Zealand’s forest research institute Scion and France’s prestigious engineering school ENSAM, began with a straightforward goal: improving quality control for glulam beam production. What emerged was a story of cross-cultural exchange and technical innovation.
“It’s not often students get to work between research and industry,” Jean said, describing his split time between Techlam’s factory floor and Scion’s research facilities. “The first impressions were overwhelming, but the constant support from both Scion and Techlam teams made all the difference.”
Jean’s background made him particularly suited for the role. Having visited more than 20 countries with his teacher parents when he was younger, he developed an adaptability that proved valuable in New Zealand’s wood industry – an environment quite different from his European experience.
At Techlam, Jean’s primary focus was refining the company’s quality assessment methods. He spearheaded the implementation of a non-destructive testing device that could evaluate glulam beam stiffness without compromising structural integrity. The system allows technicians to assess beam strength more efficiently while maintaining production quality.
His work extended to the factory floor, where he conducted a comprehensive two-month analysis of production workflows. Working alongside manufacturing teams, Jean mapped out each step of the glulam manufacturing process, identifying bottlenecks and suggesting improvements to enhance consistency.
The research component of his role at Scion proved equally substantial. Jean devoted significant time to investigating hybrid beam technology, exploring how incorporating exotic woods and carbon fibres could enhance beam performance. This research aimed to push the boundaries of traditional glulam capabilities while maintaining practical manufacturing feasibility.
“Each day brought different challenges,” Jean explained. “One day I might be calibrating testing equipment, the next analysing production data, and the next running laboratory tests at Scion. This mix of practical and research work helped me grow my skillset tremendously.”
“In Europe, the building industry doesn’t rely as much on wood, or rather in a different way” Jean noted, highlighting a key difference between the regions. This observation carries weight, considering New Zealand’s significant forestry sector. According to the New Zealand Ministry for Primary Industries, the industry generated around $6.6 billion of annual gross income in the recent years, with volumes expected to be high for the decade (to 2030) as forests planted in the past are now reaching maturity.
ENSAM’s reputation for excellence in engineering education played a crucial role in the success of this international partnership. The institution’s approach goes beyond theoretical knowledge, emphasising practical problem-solving and project leadership skills that translate directly to industry needs.
Brett Hamilton, Techlam’s Managing Director, has been particularly impressed with this practical focus: “Jean’s ability to combine theoretical knowledge with practical problem-solving has brought a new dimension to our operations.”
Having completed his internship, Jean Margerie is now finishing a full-time position at Techlam. When asked about his long-term plans, he sees part of his future in New Zealand. “I could easily see myself here for quite a few years,” he said, though he added with a laugh, “but I do miss proper French cheese.” His openness to staying in New Zealand reflects both the opportunities he sees in the country’s wood industry and the welcoming environment he’s found since arriving.
For Techlam, the collaboration with Scion and ENSAM represents an investment in both innovation and the future of engineered wood technology. As New Zealand’s engineered timber industry continues its rapid growth, partnerships like these may become increasingly important for bridging global expertise and local innovation.
// Need Techlam specs quickly for your project? Find them on Masterspec!
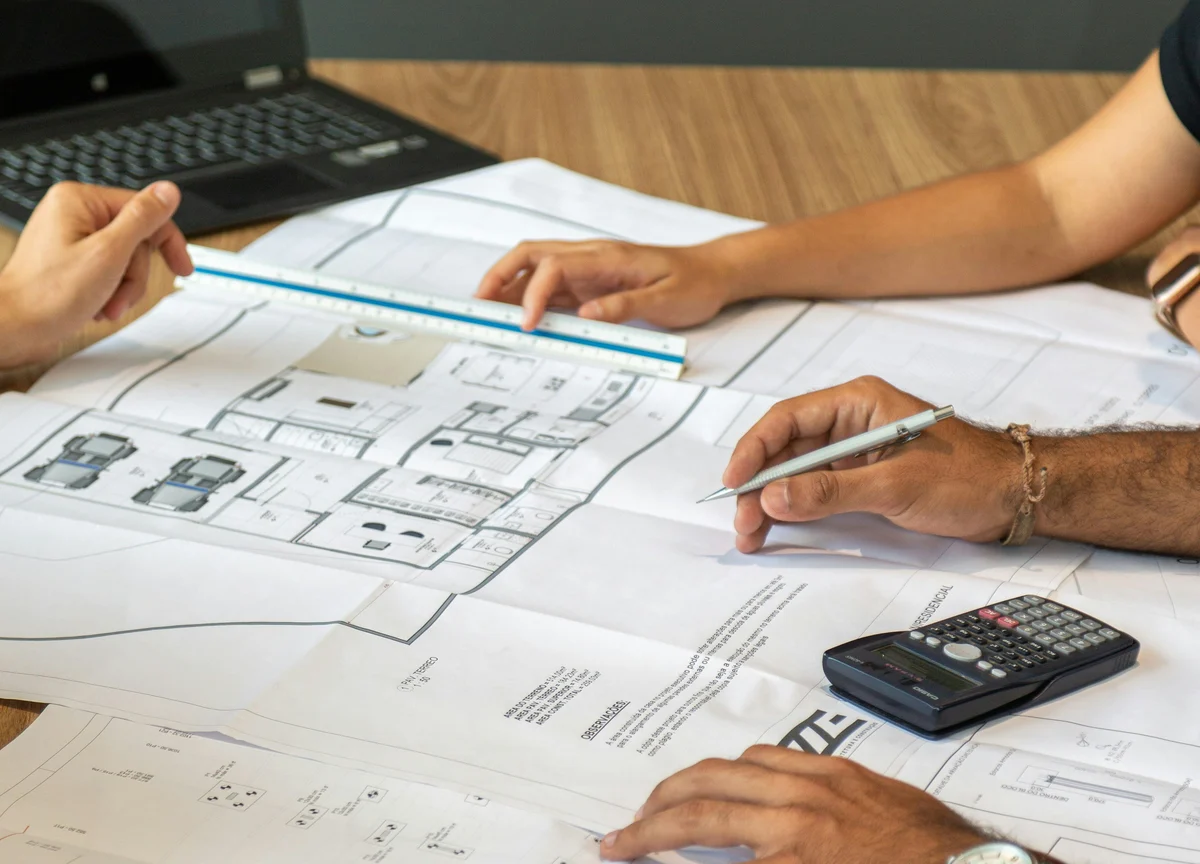
Remember, when you’re drafting specifications for your projects, Techlam’s resources are readily available on Masterspec! It simplifies things, giving you access to product details, CAD drawings and installation guides.
So, if you need to quickly specify Techlam products, it’s a handy place to find everything in one spot!
// Laminated round poles – customisable, strong and striking
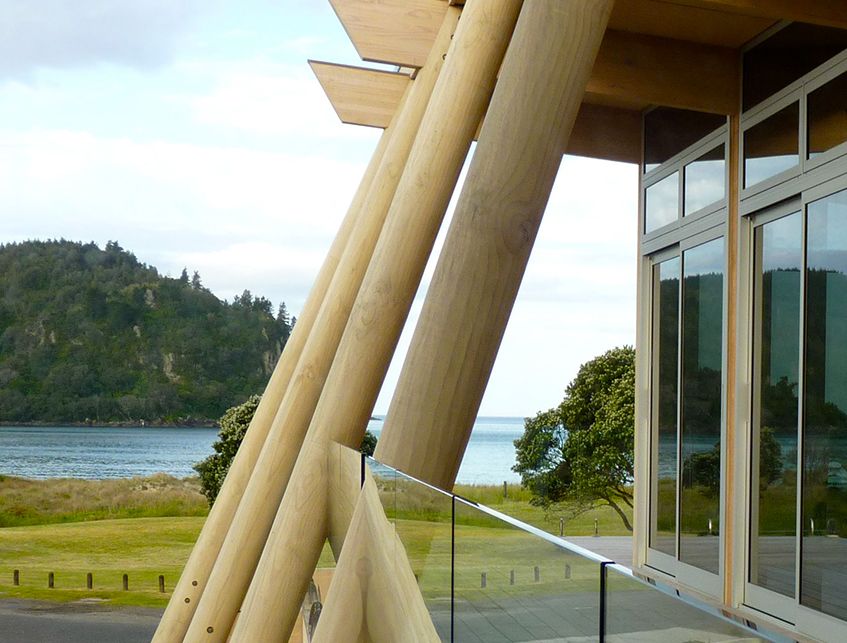
For those seeking a blend of strength and visual appeal, consider the laminated round pole. These poles, frequently overlooked, offer a distinctive advantage in project stability and aesthetics.
Dry laminated timber significantly reduces the likelihood of cracking and bending, a common issue with traditional round posts. Techlam laminated poles are adaptable, produced in virtually any length or diameter required.
Whether your project is internal or external, these poles deliver. With production capabilities reaching diameters of 1.2m, they are manufactured and machined on our plant.
The result? A pre-sanded, pre-coated product, ready for site assembly.
// Drawing strength from nature for our premium structural glulaminated timber
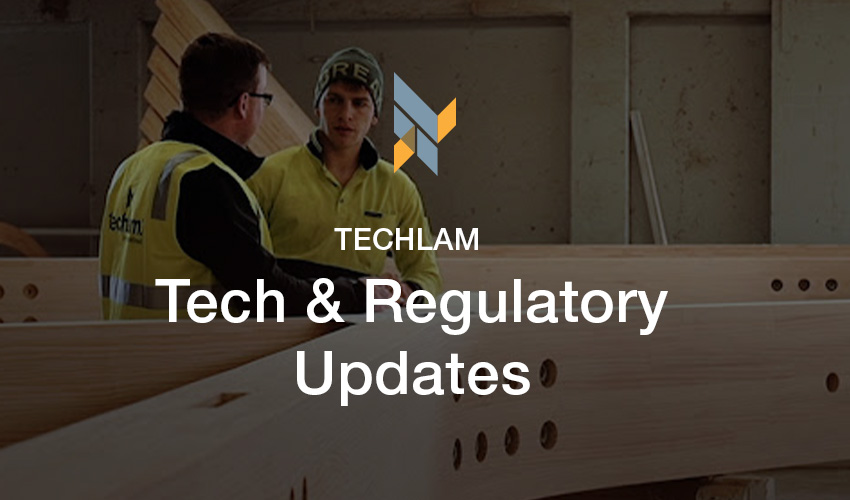
Techlam sources four different feedstock options from which we manufacture our glulam timber products. Irrespective of the lamella used, the structural performance of each is equivalent, and will create glulaminated timbers with different aesthetic qualities and a differing environmental impact. This means that Techlam can supply glulam timber products suitable for any application.
- Pinus Radiata
Pinus Radiata has a consistent quality and is known as one of the world’s best clear woods. It’s bright, white timber has a uniform appearance with little colour variation between pieces (high staining suitability), and its texture is relatively even and uniform, making it a perfect choice for applications.
Pinus Radiata is not durable and requires treatment to achieve 50-year durability. Here at Techlam, we offer two treatment options. The first relies on the traditional chemical approach as specified in NZS3640:2003. For H1.2 we offer boron-based treatments, and for hazard classes greater than H1.2, we offer CCA or MCA. Whilst its efficacy is well accepted, so is the potential environmental damage from the chemicals in the treatment.
- Accoya
To that end, Techlam offers Accoya—a Radiata Pine lamina treated with a non-toxic wood modification process that chemically modifies the timber’s cell structure (acetylation), with any residual byproducts removed to ensure its non-toxicity. Acetylation is more environmentally sustainable than traditional treatment protocols; suppliers of Accoya lamina use sustainably sourced timber and have global environmental accreditations. Unlike traditionally treated timber products, Accoya may be recycled.
- Picea Abies (commonly referred to as Spruce, or Norwegian Spruce)
Picea Abies, grown in Europe, has a creamy white appearance with a hint of yellow and/or red, with a fine, even texture and a consistently straight grain. Its light, clean appearance is sophisticated and simple, especially when stained or finished well, making it a versatile choice for various applications.
We introduced Sprucelam®, manufactured from Picea Abies lamina, to fill a gap in the New Zealand market for Scandinavian-looking interior structural timber members. Sprucelam® is untreated and so must always be left exposed.
- Pinus Taeda (commonly referred to as Loblolly Pine)
Pinus Taeda is a rapidly growing pine, native to the Southeastern United States. It has an appealing warm, yellowy tone with a straight grain and a fine to medium texture.
Pinus Taeda is only rarely grown in NZ.
However, Techlam has found that lammella from Pinus Taeda is more likely to achieve a higher structural grading than a Pinus Radiata equivalent. This means that by using Pinus Taeda for the higher strength beams, tighter timeframes can be met, especially for wider sections.
Techlam offers Pinus Taeda treated in accordance with the same standard (NZS3640) that applies to their Pinus Radiata glulam products – boron for H1.2 and CCA or MCA for higher hazard classes. Pinus Taeda falls within the scope of NZS3640. Our view is that if compliance with NZ3640 ensures radiata pine is resistant from decay for at least 50 years, then the same level of resistance will apply to Pinus Taeda.
Techlam has their own in-house regulatory expert who can be contacted at louise.swann@techlam.co.nz.
// Techlam Team Lunch 🍖
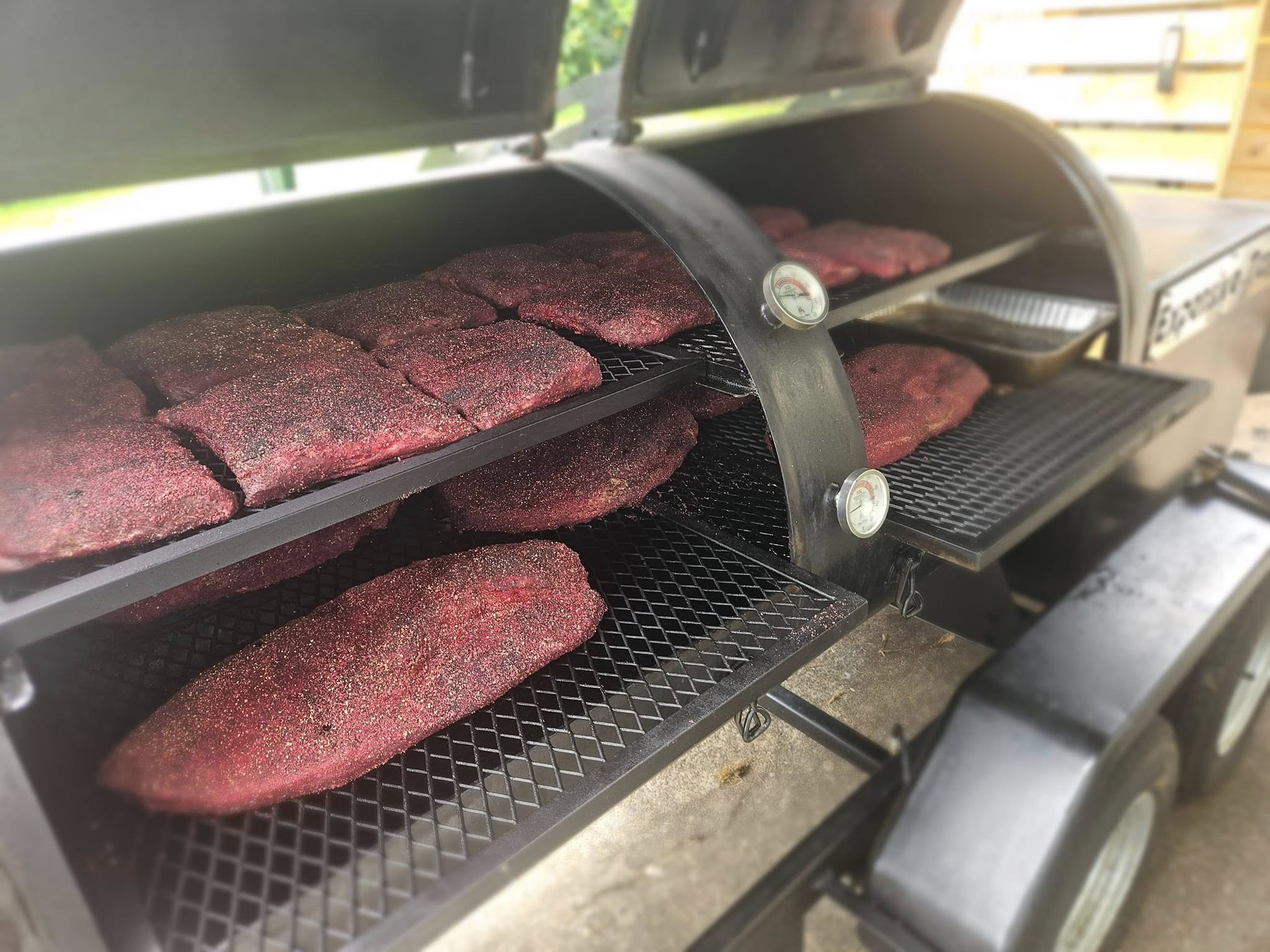
The year’s end called for a celebration, and we marked it with a staff lunch just before summer break that featured outstanding smoked BBQ from ROA SMOKED BBQ. If you happen to be in the Levin area, we’d suggest giving them a try. They offer a unique blend of Texan and Southern Carolina influences, with a Kiwi twist.
A hearty thank you goes out to the Techlam team. Their hard work, dedication and positive attitudes throughout the year have been nothing short of inspiring.